Fragen & Antworten
Enclosure Customization
FIBOX CUSTOMISING SERVICES
MACHINING SERVICE: Fibox employs state-of-the-art machines to manufacture your custom-made enclosures with drills, knockouts or openings – even for small piece numbers.
ASSEMBLY SERVICE: Have you ordered hinges, inspection windows or other Fibox accessories? Do you know our assembly service can deliver your enclosure and accessories pre-assembled and ready for use. This cuts down your labour costs and time to delivery.
TOOL MODIFICATIONS FOR OEM ENCLOSURES: Instead of having to manufacture a whole new tool Fibox can modify our own standard tools according to your OEM enclosure specification. This results in a shorter product development time and enables you to take your product to market earlier. Modifications of our standard tools give you a possibility to differentiate your products form your competitors.
COLOURED ENCLOSURES : Paint your enclosures in your corporate colour. Fibox offers customers a choice of custom or RAL colour for plastic enclosures, even for relatively small quantities.
LACQUERED ENCLOSURES: Fibox provides a lacquer coating for your enclosures on request. This process is especially recommended for production quantities of under 500 pieces. We offer a comprehensive range of lacquer options.
EMC PROTECTION FOR ENCLOSURES: Fibox can provide your plastic enclosure with EMC protection if desired. For example we can apply a conductive copper coating to the inside faces, or utilising a special conductive gasket....or both.
PRINTED ENCLOSURES: Fibox can supply your enclosures with silk screen printing to your specification. Smooth, even surfaces are required.
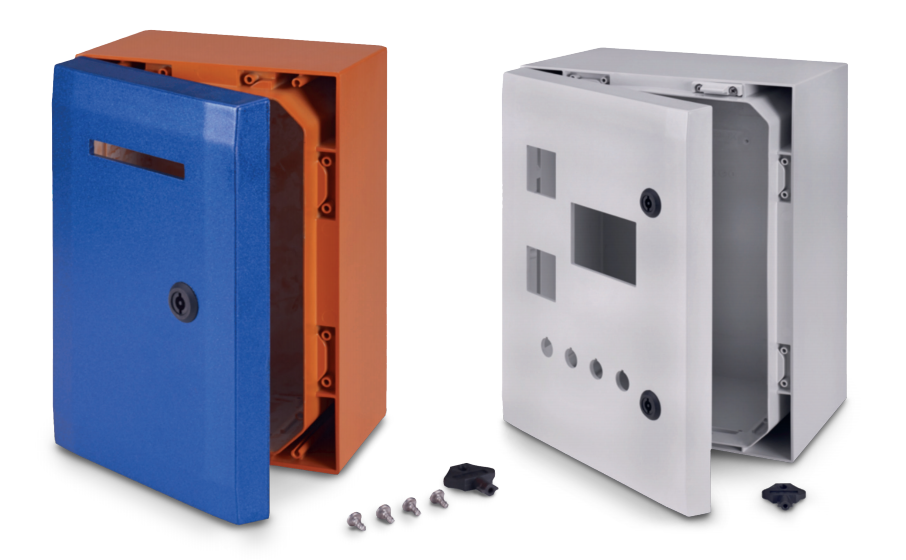
IP and IK classification
Ingress protection class of enclosures is given in form of IP classification, a two-digit coding which is shown below. Fibox has tested the enclosures according to IEC 529 or EN 60529. The latter requires the second digit to be tested from class 6 upwards separately to each level of class, thus the double marking IP 66 / IP 67 indicates that the actual tests have been made for both levels.
The European standard for enclosures, EN 50298 also includes IK impact test. This test is described in EN 50102. The data for impact resistant is available for each individual Fibox enclosures.
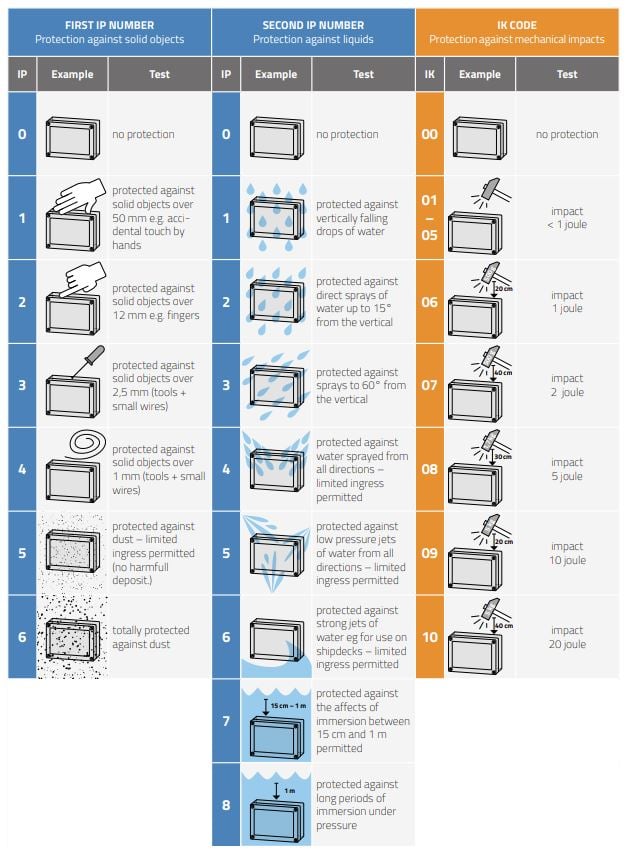
NEMA and UL classification
NEMA CLASSIFICATIONS OF PROTECTION
The National Electrical Manufacturers Association (NEMA) is a US Manufacturers Organisation that actively promotes standardized product specifications for electrical apparatus.
NEMA performance criteria and test methods are used by Underwriters' Laboratories as guidelines for investigation and listing of electrical enclosures. Approximate IP equivalents in parentheses
NEMA |
Indoor use primarily to provide a degree of protection against contact with the enclosed equipment and against a limited amount of falling dirt. (IP30) |
2: |
Indoor use to provide a degree of protection against limited amounts of falling water and dirt. (IP31) |
3: |
Outdoor use to provide a degree of protection against windblown dust, rain, and sleet; undamaged by the formation of ice on the enclosure. (IP64) |
3R: |
Outdoor use to provide a degree of protection against falling rain and sleet: undamaged by the formation of ice on the enclosure. (IP32) |
3S: |
Outdoor use to provide a degree of protection against windblown dust, rain and sleet; external mechanisms remain operable while ice laden. |
4: |
Indoor or outdoor use to provide a degree of protection against splashing water, windblown dust and rain, hose directed water; undamaged by the formation of ice on the enclosure. (IP66) |
4X: |
Indoor or outdoor use to provide a degree of protection against splashing water, windblown dust and rain, hose directed water; undamaged by the formation of ice on the enclosure, resists corrosion. (IP66) |
6: |
Indoor or outdoor use to provide a degree of protection against the entry of water during temporary submersion at a limited depth; undamaged by the formation of ice on the enclosure. |
6P: |
Indoor and outdoor use to provide a degree of protection against the entry of water during prolonged submersion at a limited depth. |
11: |
Indoor use to provide by oil immersion a degree of protection of the enclosed equipment against the corrosive effects of corrosive liquids and gases. |
12,12K: |
Indoor use to provide a degree of protection against dust, falling dirt and dripping noncorrosive liquids. (IP65) |
13: |
Indoor use to provide a degree of protection against dust and spraying of water, oil and noncorrosive coolants. (IP65) |

Enclosure materials
POLYCARBONATE (PC)
Standard polycarbonate (PC) or Glassfibre reinforced (PC+GLAS)
Benefits:
|
Drawbacks:
|
ABS (Acrylnitrile-butadiene -styrene)
Benefits:
|
Drawbacks:
|
GRP - GLASS FIBRE REINFORCED POLYESTER
Benefits:
|
Drawbacks:
|
Polycarbonate and ABS enclosure materials
The FIBOX thermoplastic enclosures are made of polycarbonate (PC) or acrylnitrile-butadiene-styrene (ABS) materials. High impact-resistant polystyrene (PS) enclosures are available to order.
Polycarbonate is an amorphous thermal plastic material whose high heat resistance and excellent physical properties make it an ideal material for enclosures. Polycarbonate can withstand a wide range of temperature fluctuations and its good electrical properties are unaffected by humidity. As a self-extinguishing material polycarbonate requires no protective coating.
ABS is another amorphous thermal plastic material with good physical properties and high resistance to chemical attack. It is an ideal cost effective material.
UV resistance of Fibox enclosures polycarbonate, transparent and grey
Virtually all plastic materials are susceptible to degradation under the influence of U.V. radiation, but the quality polycarbonates used in FIBOX enclosures show high durability in this respect, too.
In European latitudes FIBOX enclosures can be used, without hesitation, in outdoor applications. Over the years a slight discoloration, especially of the transparent cover material, will occur. If this must be avoided, a sun roof is recommended.
In tropical latitudes the grey coloured material still performs with only some discoloration. This is due to the TiO used in the grey pigmentation in order to UV-stabilize the material. The transparent material, however, which absorbs the U.V. radiation throughout the material, will in due time (some years) not only turn yellowish, but the high impact resistance will decrease, see below. But more than lowering the impact resistance, the transparent materials allow the UV-radiation to detonate the components mounted inside the enclosure.
The polycarbonates used in FIBOX enclosures have been tested and approved by Underwriters Laboratories, Melville, N.Y. USA, in conformity with standard UL 508 par. 34; 16-22. This standard specifies testing 720 hours in ‘Weatherometer’ (intensified UV light combined with water spray). After testing the materials must retain 85% of the original values with respect to tensile and flexural strength, impact resistance, flammability, and glow wire ignition
UV resistance of Fibox enclosures ABS
ABS materials are less protective against UV rays if directly exposed, can be used if protected against weather influences.
Maintenance of polycarbonate and ABS enclosures
Polycarbonate and ABS enclosures require no actual maintenance. Any dusty units can be cleaned with soap and water. If a detergent is used, the enclosure should be thoroughly rinsed in clean water. Do not use any solvents.
Cast AISi aluminium (AL)
Benefits:
|

Enclosure materials - comparison
Comparison of materials
The following table gives a general idea of the properties of the various materials. For more detailed information on material performance in your specific application environment please consult your local FIBOX representative.
**** = Excellent
* = Poor
1) Polyester powder coated AISi cast aluminium
2) Glass fibre reinforced
Property |
PC |
ABS |
GRP |
AL1) |
PA62) |
NORYL |
PS |
General properties | |||||||
Outdoor use |
**** |
*** |
***** |
**** |
**** |
* |
* |
Indoor use |
***** |
***** |
***** |
***** |
***** |
***** |
***** |
Cost |
*** |
***** |
* |
* |
** |
*** |
***** |
Light weight |
***** |
***** |
*** |
* |
***** |
***** |
***** |
High rigidity |
*** |
* |
**** |
***** |
*** |
*** |
* |
Impact resistance |
***** |
*** |
**** |
**** |
*** |
*** |
* |
Chemical Resistance |
|||||||
Salt water environments |
***** |
** |
***** |
****1) |
***** |
***** |
** |
Neutral salts |
***** |
***** |
****1) |
**** |
***** |
**** |
|
Acids, low concentrations |
***** |
**** |
***** |
** |
**** |
**** |
**** |
Acids, high concentrations |
*** |
* |
*** |
* |
* |
**** |
* |
Alkalis, low concentrations |
*** |
***** |
**** |
* |
** |
**** |
***** |
Alkalis, high concentrations |
* |
**** |
**** |
* |
* |
*** |
**** |
Petroleum |
*** |
* |
***** |
***** |
**** |
* |
* |
Hydraulic oil |
***** |
***** |
***** |
***** |
***** |
***** |
|
Alcohols |
**** |
*** |
**** |
***** |
**** |
*** |
|
Solvents |
* |
* |
***** |
***** |
* |
||
Cooling fluids |
*** |
***** |
***** |
*** |
***** |
Data subject to change without notice.
Gasket Materials
FIBOX ENCLOSURE GASKETS OFFER THE BEST PROTECTION
Gasketing plays an essential role in enclosure protection. In the long run, the IP rating and its reliability depend mainly on the properties of the gasket used in the enclosure. Key performance factors of a gasket are its compression set and proper fit in the gasket groove. The best general purpose gasket material is polyurethane which has an exceptionally low compression set. When accurately injection foamed, the polyurethane gaskets stay tightly in the right place. And EPDM material provides the best protection against the most popular industrial chemicals. However, it is wise to check the effect of a chemical on each gasket material since the chemical resistance of gasket materials varies greatly.
In some cases the performance of an enclosure can be mod ifed by changing its gasket. The degree of protection depends on the material and the cross-section profile of the gasket. When choosing gasket material, compare the elasticity properties of different materials and how these properties are affected by cold and heat, or by contact with various chemicals. An important factor is that both the enclosure and gasket must withstand the same chemicals in order to reach a safe resistivity.
FIBOX ENCLOSURES ARE WELL DESIGNED
The degree of ingress protection (IP) of an enclosure is mainly dependent on the properties of its gasket. Nevertheless, the gasket must also properly fit the enclosure. In addition to the cross-section profile of the gasket, there is the cross section of the gasket’s contact with the surfaces of the enclosure bases and covers. If the cross-section structures and manufacturing accuracy of an enclosure are not top quality, the IP rating will remain low even when equipped with a good gasket. Naturally, all FIBOX enclosures are carefully designed and precision made. Using FIBOX enclosures, you only need to focus on the variances in gasket materials.
FIBOX enclosure gaskets are made of PUR, EPDM, neoprene and silicon materials. Table 1 includes some commonly-used physical properties of the gaskets. Note that the chemical resistances in the box and in Table 2 are only rough generalizations to give you some clues to gasket material behavior. The resistance of each chemical should be checked separately. For additional information, please contact Fibox.
Table 1: Gasket materials: physical properties comparison
Property |
Unit |
TPE |
PUR |
EPDM |
Neoprene |
Silicon |
Temperature range |
°C |
-40 - +120 |
-50 - +130 |
-50 - +120 |
-40 - +100 |
-60 - +170 |
Tensile strength |
Mpa |
5 |
0,4 |
13,0 |
8,0 |
9,4 |
Elongation at break |
% |
700 |
110 |
300 |
250 |
540 |
Hardness |
Shore A |
30 |
12 |
65 |
66 |
52 |
Density |
g/cm3 |
1,13 |
0,33 |
1,12 |
1,6 |
1,15 |
Compression set |
% |
17 |
5 |
20 |
35 |
14 |
Table 2: Gasket materials: physical properties comparison
Chemical Performance |
TPE |
PUR |
EPDM |
Neoprene |
Silicon |
Neutral salts |
**** |
**** |
**** |
**** |
**** |
Acids, low concentrations |
**** |
*** |
**** |
*** |
*** |
Acids, high concentrations |
*** |
* |
*** |
* |
* |
Alkalis, low concentrations |
**** |
*** |
**** |
**** |
*** |
Alkalis, high concentrations |
*** |
* |
**** |
*** |
* |
Petroleums |
* |
* |
* |
*** |
* |
Hydraulic oils |
* |
**** |
* |
*** |
* |
Alcohols |
** |
*** |
**** |
**** |
**** |
Cooling fluids |
*** |
*** |
**** |
*** |
**** |
Flammability Classification - UL 94
UL 94 FLAMMABILITY CLASSIFICATION TESTS FOR PLASTIC MATERIALS
UL 94 is the standard applied by the American Underwriters Laboratories for the testing of the flammability and fire safety of plastic materials used in devices and appliances. In the UL 94 HB (Horizontal Burning) test the burning of a horizontal plastic specimen is tested and in the most demanding UL 94V (Vertical Burning) tests the burning of a vertical test specimen. Precise details of the equipment, conditions and test systems to be used can be found in the UL 94 standard.
UL 94 HB: Horizontal burning test
The length of the test specimen is 5" (127 mm) and width 0.5" (12.7 mm). The test sheet cannot be more than 0.5 (12.7 mm) thick. Lines are marked on the sheet at the 1" and 4" locations. The sheet is fixed horizontally at one end and tilted 45 degrees in the direction of the width, as shown in the diagram. The burner used is adjusted so that it forms a 1" long blue flame. The flame is directed at an angle of 45 degrees to the front edge of the plastic sheet so that about 1/4 of the test specimen’s front edge is in the flame. The flame is applied for 30 seconds, after which it is removed. If the test specimen burns to the 1" line before 30 seconds have passed the flame is removed immediately. The test is carried out on three test sheets.
The material under investigation is classified as UL 94 HB if, after the removal of the flame:
A) The speed of burning does not exceed 1.5" (38.1 mm) per minute when the test specimen thickness is 0,120-0,500" (3,05-12,7 mm)
or
B) The speed of burning does not exceed 3,0" (76.2 mm) per minute when the thickness of the specimen is less than 0,120" (3,05 mm)
or
C) Burning finishes before the flame reaches the 4" line
UL 94 V-0, V-1, V-2: Vertical burning tests
The test specimen length is 5" (127 mm) and width 0.5" (12.7 mm). The sheet to be tested can not be more than 0.5’ (12.7mm) thick. The sheet is fixed 1/4" from the upper end in the vertical position. A metal mesh covered with surgical cotton is positioned 12" (305 mm) beneath the test sheet. The flame of the burner used is adjusted so that is forms a 3/4" blue flame. The flame is directed from below at the lower edge of the plastic sheet at a distance of 3/8" (9.5 mm). The flame is applied for 10 seconds, after which it is removed. The burning time of the test specimen is recorded. Immediately the burning stops the flame is reapplied for 10 seconds. After removal of the flame the burning time and afterglow time is again noted. The entire test is carried out on five different test specimens.
The material tested is UL 94 V-O classified if:
A) None of the five test specimens burn for over 10 seconds at any time when the burner flame is removed.
B) The total burning time of the 10 ignition test does not exceed 50 seconds.
C) No test specimen burns either with a flame or afterglow to the clamp.
D) No burning drops should fall which would cause the cotton underneath to ignite from any test specimen.
E) The afterglow burning of no test specimen exceeds 30 seconds.
The material tested is UL 94 V-1 classified if:
A) None of the five test specimens burn for over 30 seconds at any time when the burner flame is removed.
B) The total burning time of the 10 ignition test does not exceed 250 seconds.
C) No test specimen burns either with a flame or afterglow to the clamp.
D) No burning drops should fall which would cause the cotton underneath to ignite from any test specimen.
E) The afterglow burning of no test specimen exceeds 60 seconds.
The material tested is UL 94 V-2 classified if:
A) None of the five test specimens burn for over 30 seconds at any time when the burner flame is removed.
B) The total burning time of the 10 ignition test does not exceed 250 seconds.
C) No test specimen burns either with a flame or afterglow to the clamp.
D) Only such burning pieces may fall from the test specimen, which burn only momentarily, and of which some ignite the cotton underneath.
E) The afterglow burning of no test specimen exceeds 60 seconds.
UL 94 5V: Vertical burning test
The length of the test specimen is 5" (127 mm) and the width 0.5 (12.7 mm). The test sheet shall not be more than 0.5" (12.7 mm) thick. Flammability classification is granted for specific thickness intervals, for which both the maximum thickness and minimum thickness sheet must be tested. The test sheet is fixed 1/4" from the upper end in the vertical position. The flame of the burner used is adjusted so that it forms a 5" flame whose blue heart is 1,57" (40mm) long. The flame is directed from below at the corner of the plastic sheet at a distance of 1". The flame is applied for 5 seconds, after which it is removed for 5 seconds. This is repeated five times. The entire test is carried out on five test specimen.
The material tested is UL 94 5V classified if:
A) No test specimen burns with a flame or afterglow for more than 60 seconds after the fifth ignition.
B) No material drops from the test specimen.