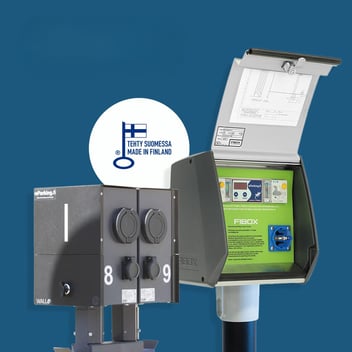
Investment in Quality Processes Recognized: Fibox Charging Solutions Receives ISO 9001 Certification
The ISO 9001 standard for quality management systems provides a solid stepping stone for the growth of Fibox's EV charging business, ensuring a systematic and organized approach across the company’s various operations.
Fibox Charging Solutions' quality management system is now certified to ISO 9001:2015 by Bureau Veritas. This certification covers the company's product development, manufacturing, marketing, and sales of electric vehicle charging and car heating products.
“The idea of building and implementing a quality management system that meets the requirements of ISO 9001 certification emerged towards the end of 2023, as we were preparing the company for its next growth phase,” says Stefan Backman, Managing Director of Fibox Charging Solutions Oy.
For customers and partners, the quality management system translates into even better products and more streamlined processes, as the company can more effectively identify business opportunities and customer needs.
“We are better able to detect changes within our organization and in the external environment, understand them more deeply, and respond to them more quickly. Above all, the system encourages us to regularly evaluate our operations and make everything more transparent throughout the organization,” Backman explains.
The certification requirements align with company needs
In the spring of 2024, the team at the Vikinraitti EV charger factory worked hard to implement the quality management system throughout the company. Already during ramp up at the factory in the spring of 2023, operational models were designed to align with ISO 9001 certification requirements, which proved a major plus during the auditing phase.
“Our processes were already in good shape even before the audit. It was important that we made improvements for ourselves rather than just for the external auditors. This helps us to commit more strongly to the agreed practices,” emphasizes R&D Manager Mika Levonen.
New Documentation Platform Enhances Transparency and Streamlines Processes
The most significant practical change was the introduction of a documentation system to facilitate the maintenance and tracking of documentation.
“We are now able to gather all documentation related to risk management, employee qualifications, and even equipment calibrations in one clear place. Process descriptions were also clarified, which adds transparency to our daily operations. For example, our emergency procedures became easier to follow due to clearer process descriptions,” explains Production and Facility Manager Toni Hakala.
Working on quality is key to open internal communication
Operating in accordance with the quality management system also leads to more open and meaningful communication throughout the organization. The certification serves as an important internal message, which, according to Backman, drives continuous development, learning, and improvement within the organization.
“Above all, the certification is a testament to ourselves that we’ve reached an important milestone in taking our operations to the next level as part of our growth journey,” Backman says.
Hakala also expresses satisfaction that their hard work is being recognized.
“From the beginning, we’ve put in a tremendous amount of effort to improve our operations, and this certification reflects the results of that work.”
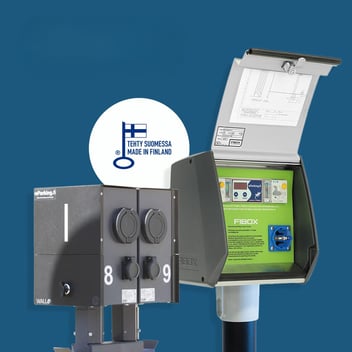
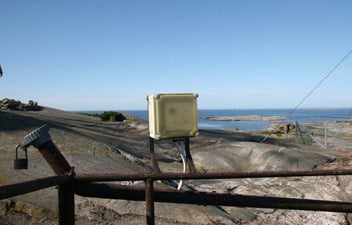
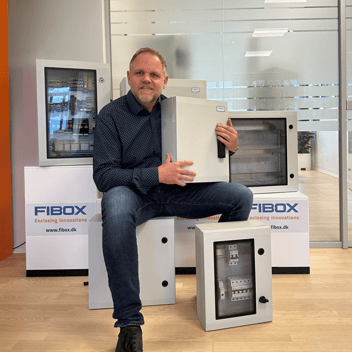
Iconic Fibox arca IEC turns 10 years
For the birthday of ARCA IEC, our most iconic cabinet, we sat down to chat with our Director of...